Small Scale Plasticity
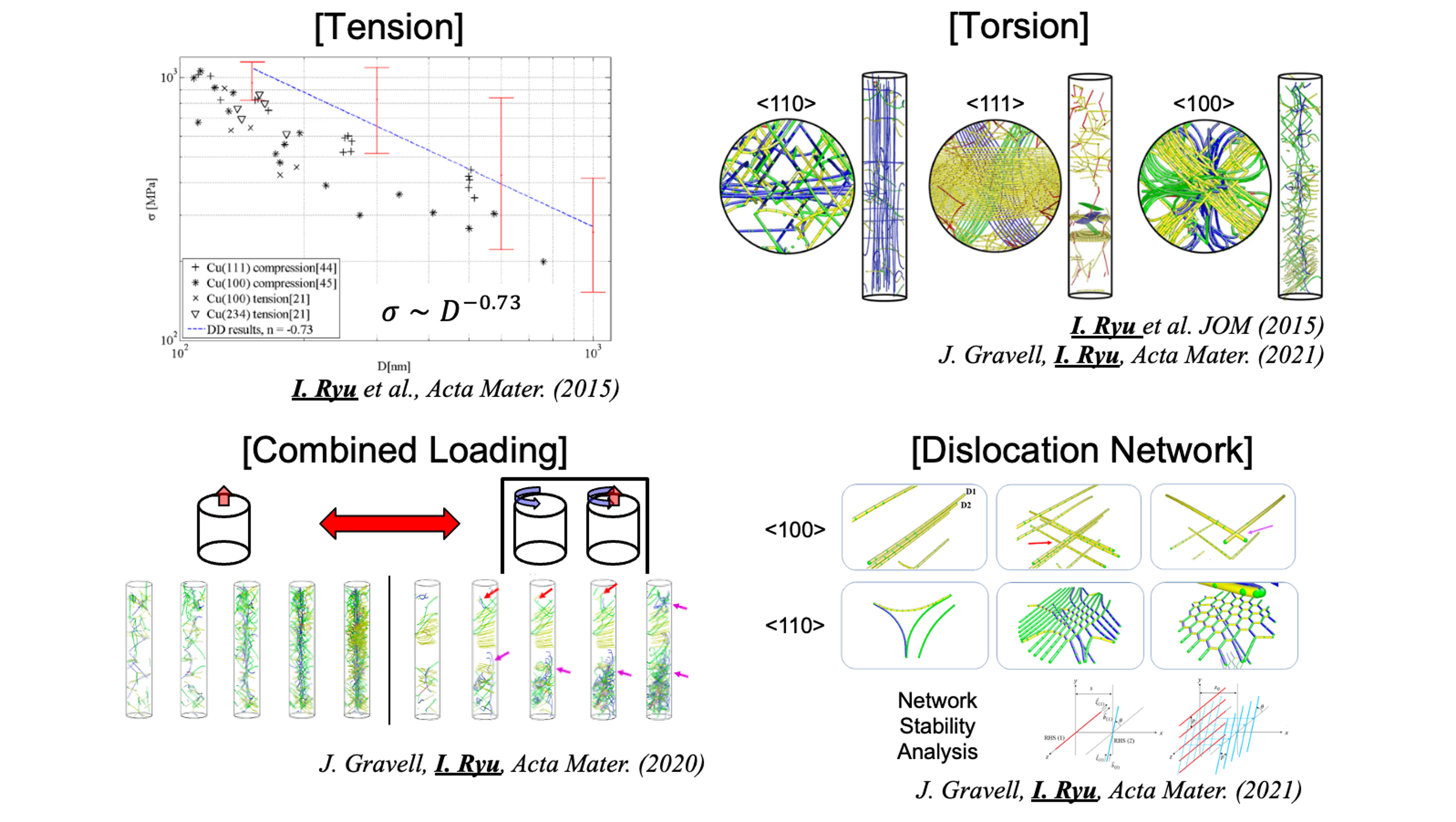
Dislocation Plasticity
Dislocation dynamics modeling could allows us to understand the physical origin for plastic deformation.
Concurrently-coupled Defect Dynamics
This concurrently coupled multi-scale plasticity model can capture detailed dynamics evolution of dislocation structures and can predict macroscopic constitutive response. In addition, the developed model could account for complex multi-physical phenomena, which would play an important role in obtaining a fundamental understanding of deformation mechanism in nanostructural metals.
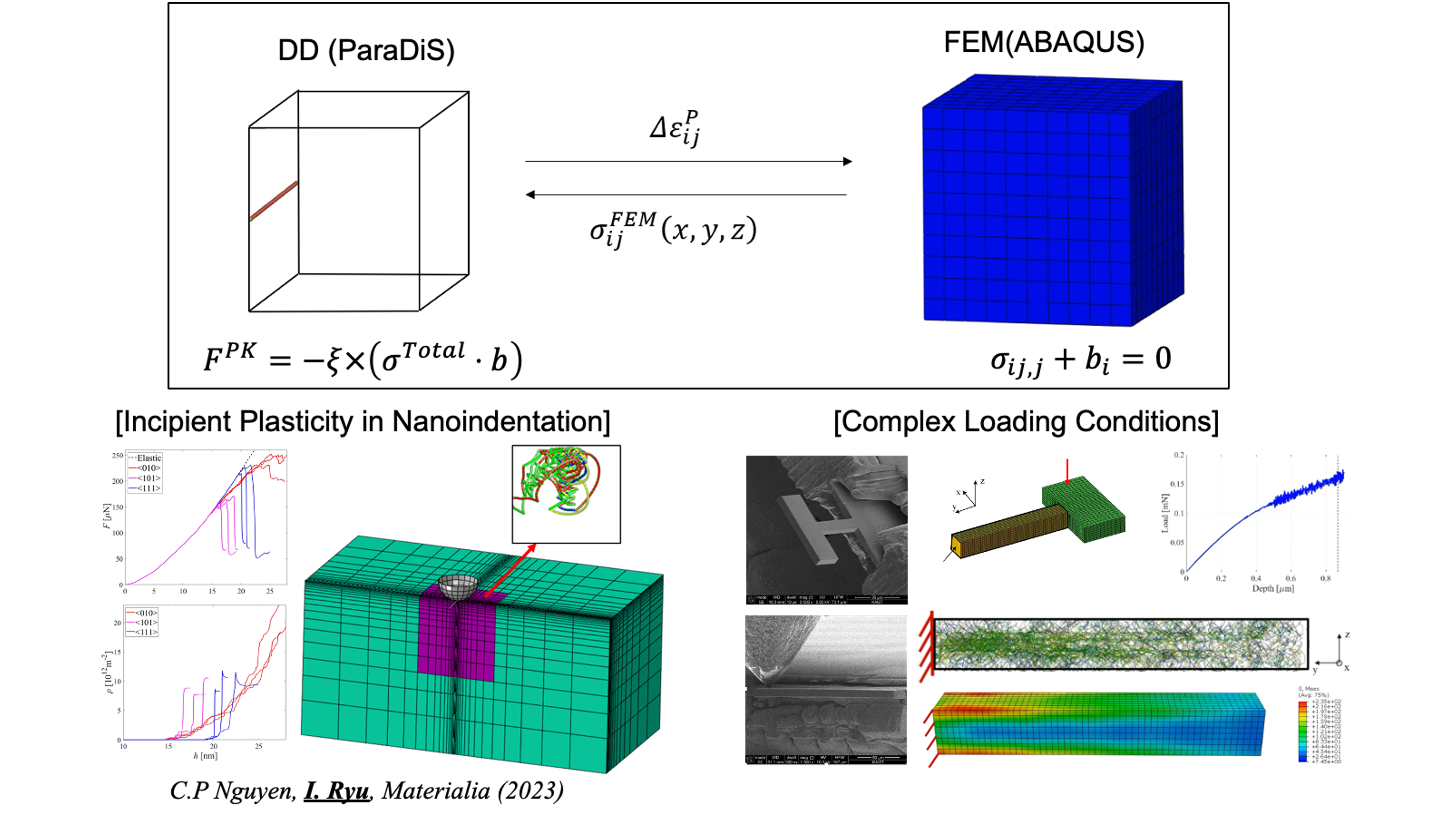
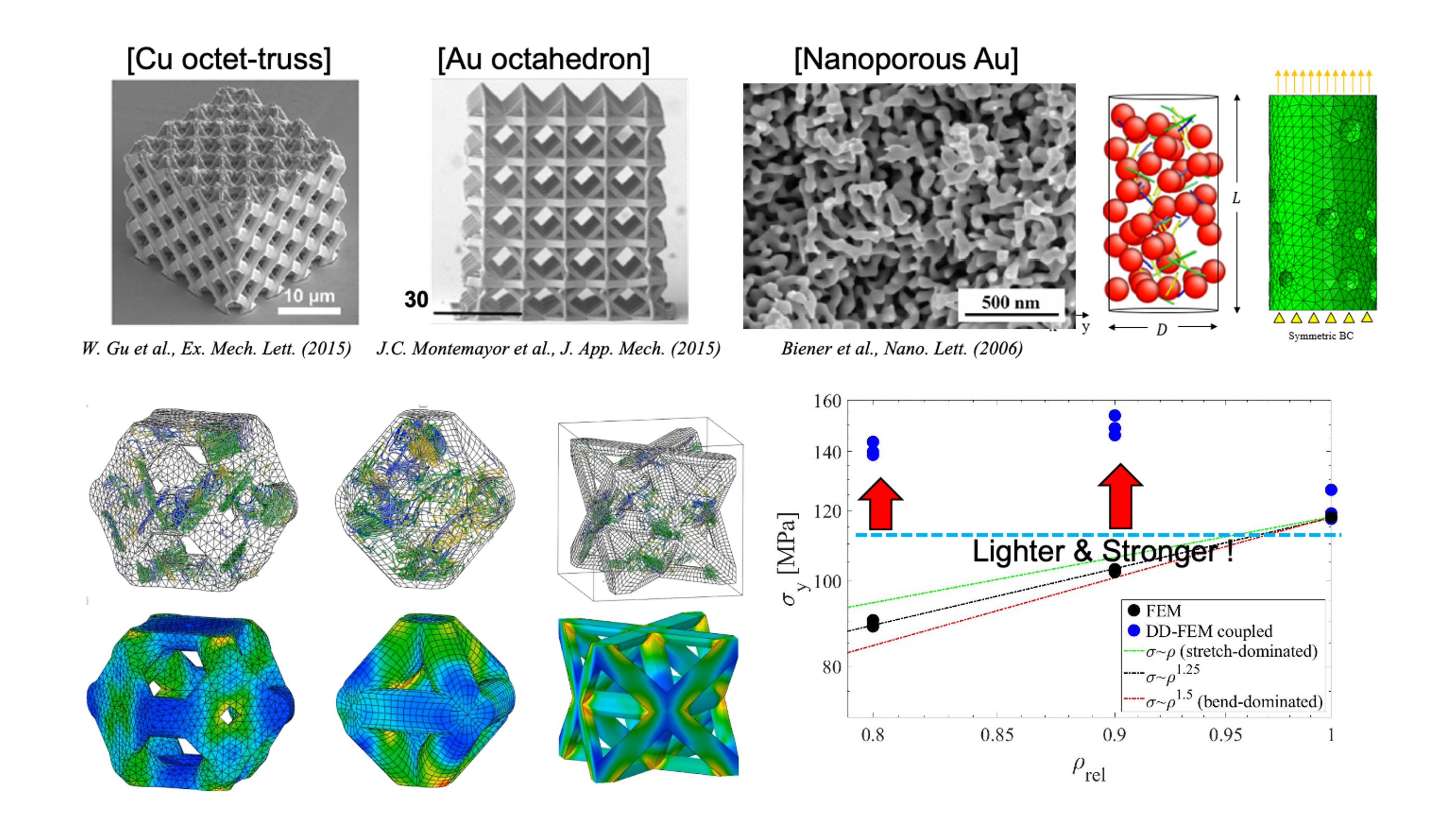
Mechanical Properties of Nanostructures
Nanostructural metals show enhanced mechanical properties. For optimal design, it is critical to understand the deformation mechanism in the microstructure.
Dislocation Interaction with Grain Boundaries
To understand the underlying mechanisms that control the mechanical properties of nanostructured metals, an insight into the role of the grain boundary in dislocation-driven plastic deformation is vital. The grain boundary has been observed as a dislocation source, sink, or having no effect, which in turn, gives rise to different macroscopic mechanical responses.
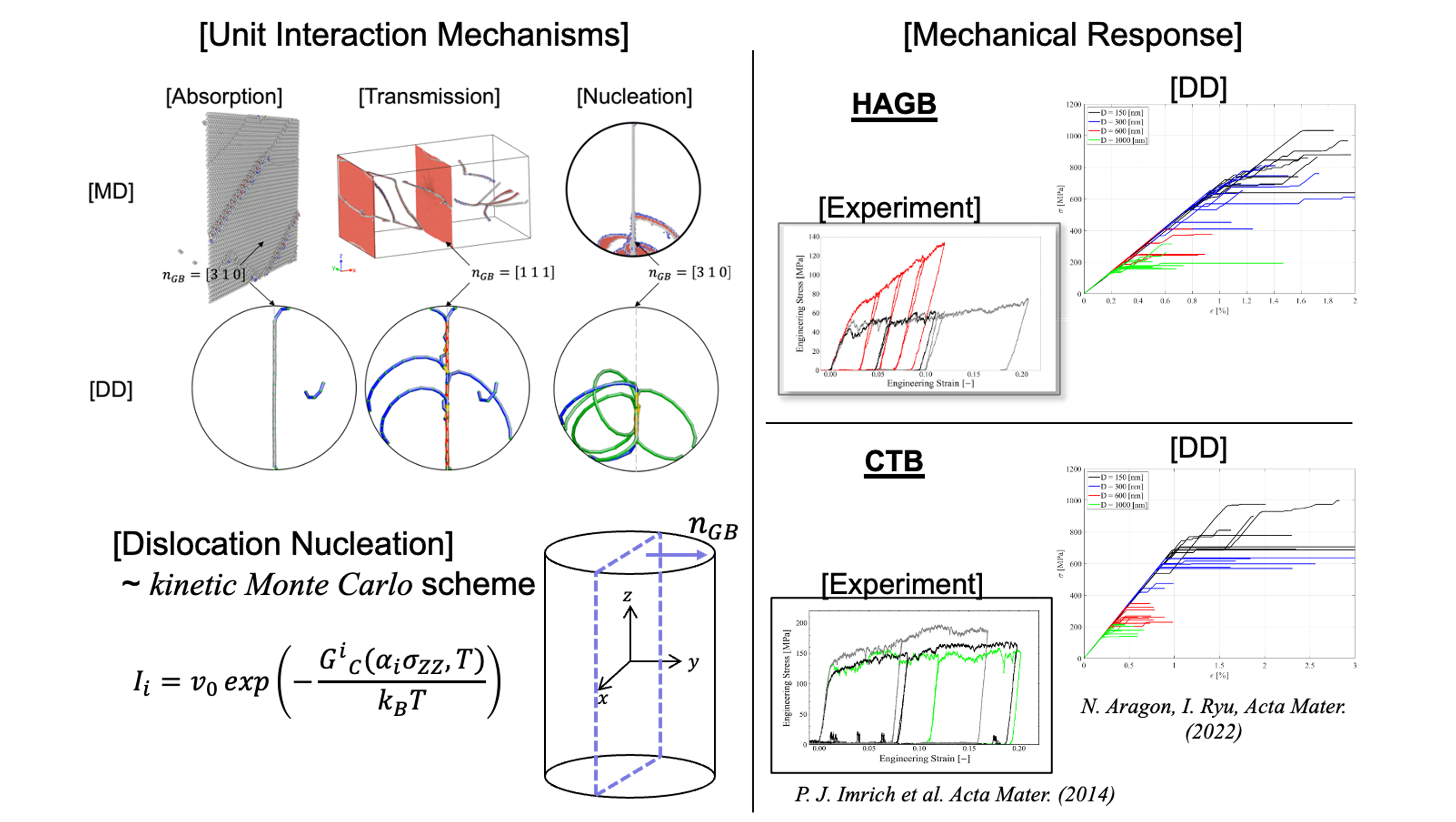
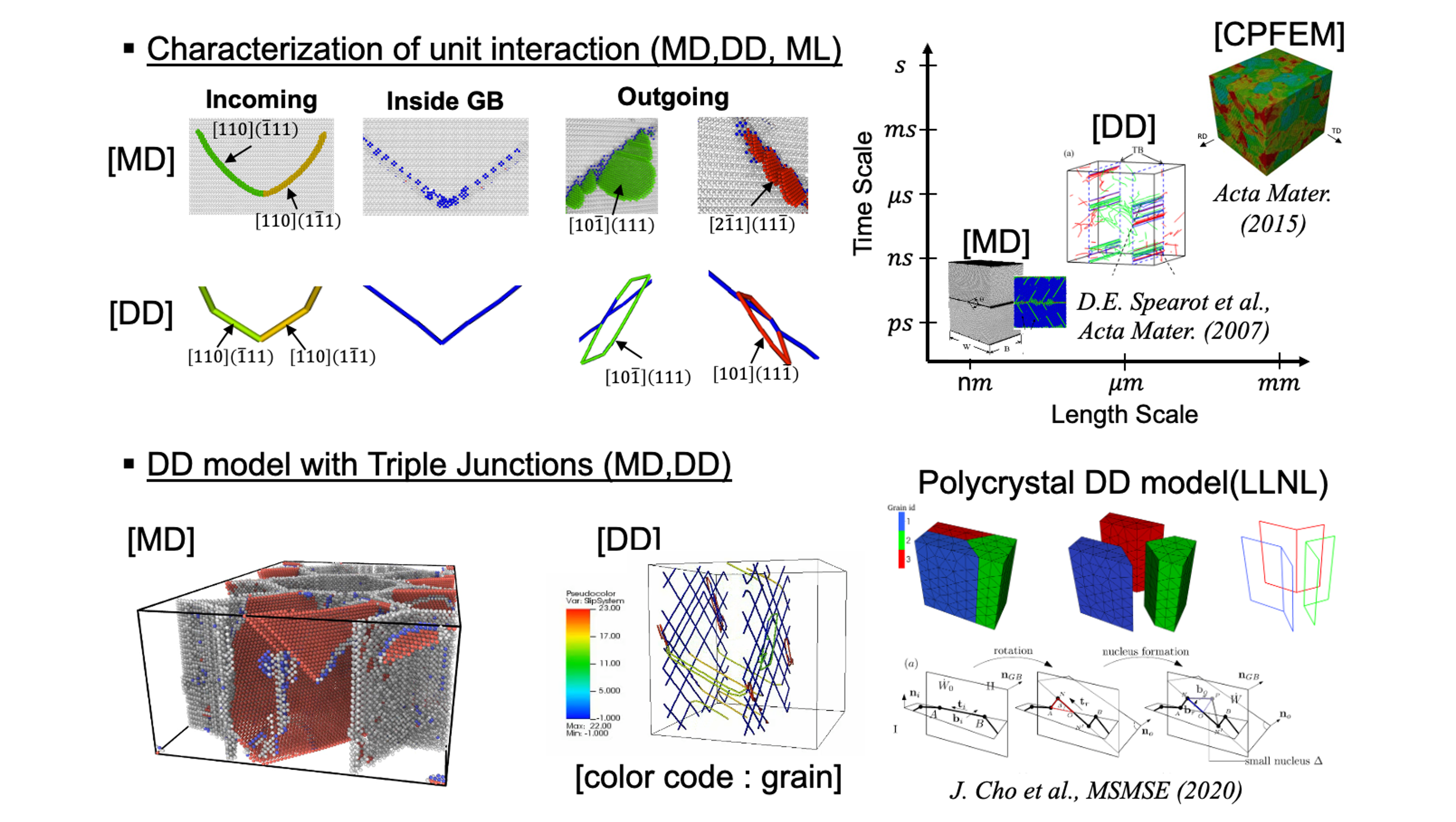
Mesoscale plasticity in Polycrystals
We propose a high-fidelty model for dislocation interaction with various grain boundary (GB), employing it to effectively capture atomistic interaction mechanism on the GB, by means of mesoscale defect dynamics model. We apply our mesoscale polycrystal plasticity model to investigate defect-driven mechanical properties.
Fracture and Damage
Materials for Extreme Environments
Materials for extreme environments can help to protect people, structures and the planet. Extreme temperatures in aeroplane engines, high-strain rate loading and hydrogen embrittlement and radiation doses in nuclear reactors are just some examples of extreme conditions that materials need to withstand. We investigate deformation plasticity under multi-physical environments for materials for different types of extreme environments.
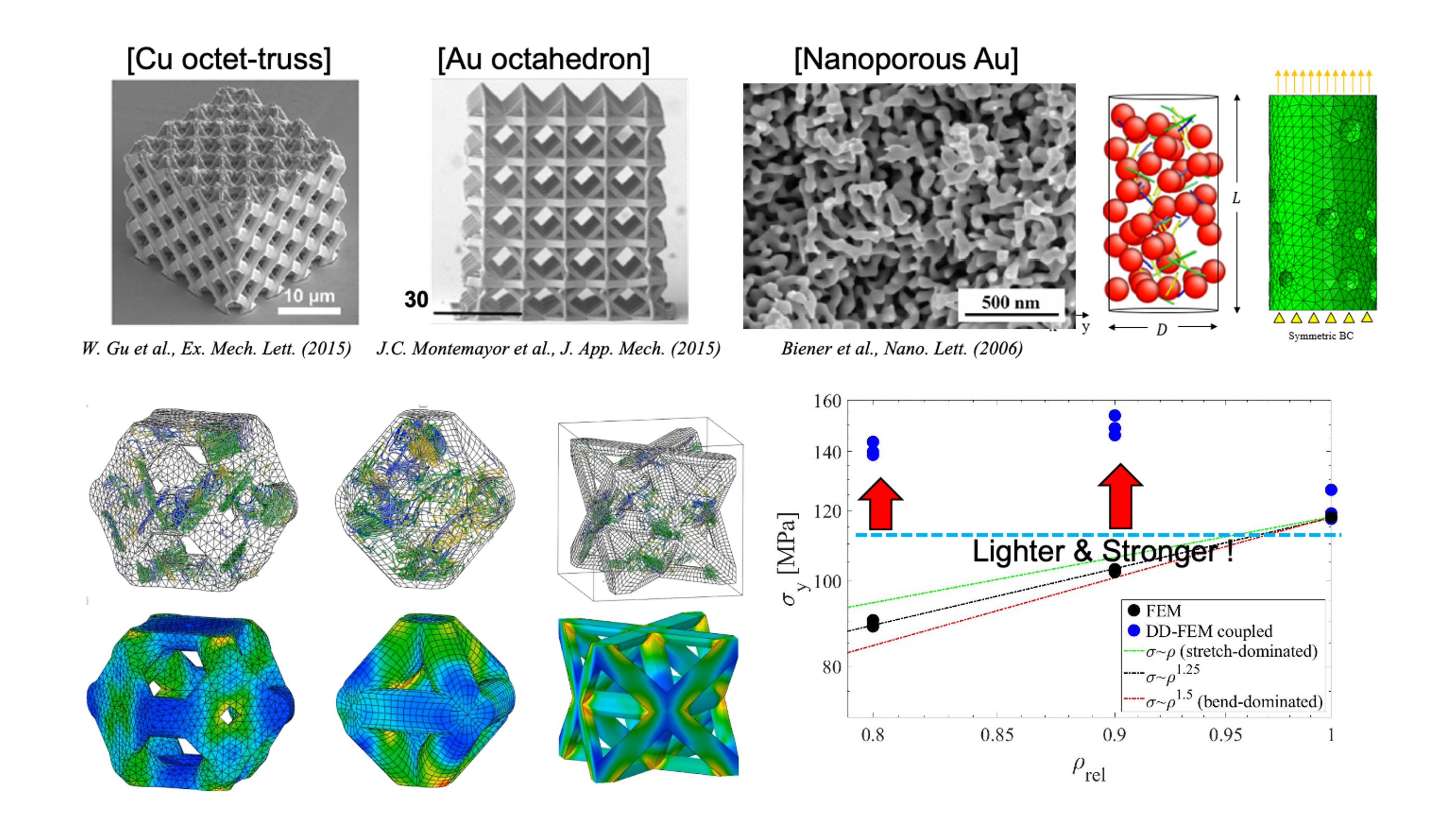
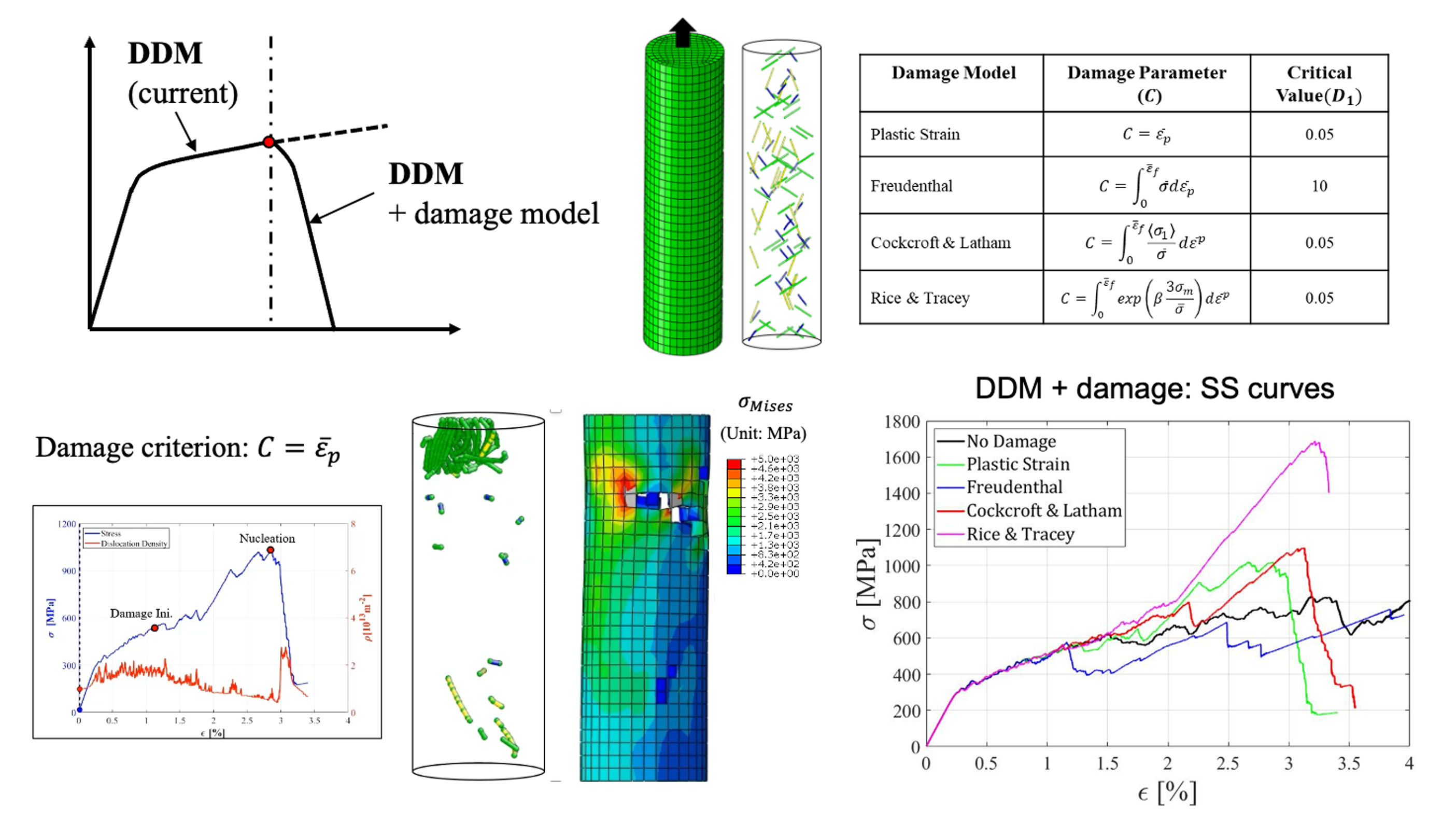
Micromechanical Damage Model
Material damage properties of crystalline materials are essential for their engineering application. Based on detailed information of defect microstructure, we investigate the micro-mechanical damage model, which could allow us to investigate failure mechanism of crystalline solids.
Reliability Analysis
High Performance Energy Storage Design
It is a great challenge to exploit suitable anode/cathode materials for high-performance energy storage. In an effort to make a physical model, we employ muliti-physics approach with mechanics , which could shed light on the mechanics of deformation and failure of energy storage during battery cycling.
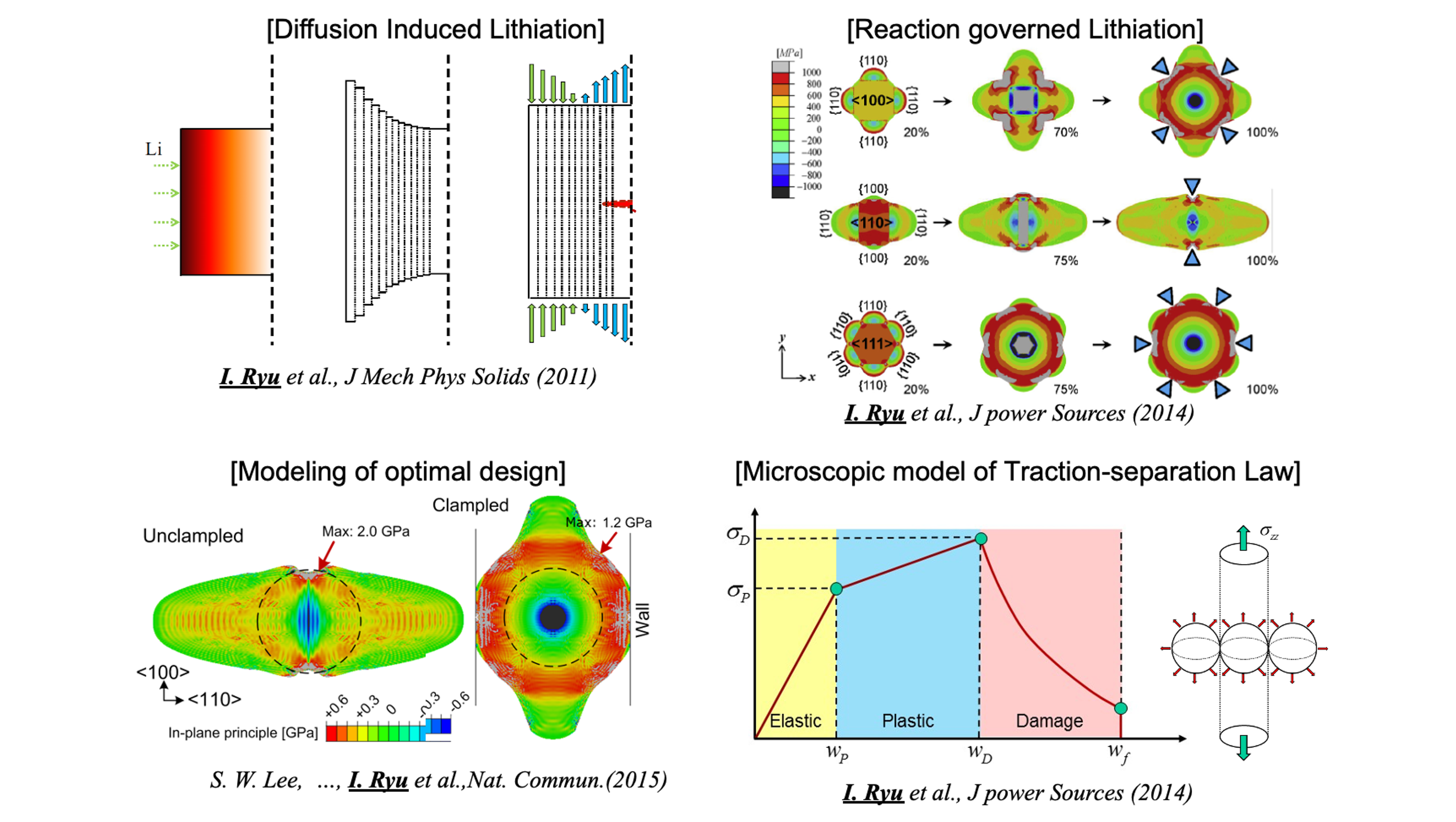
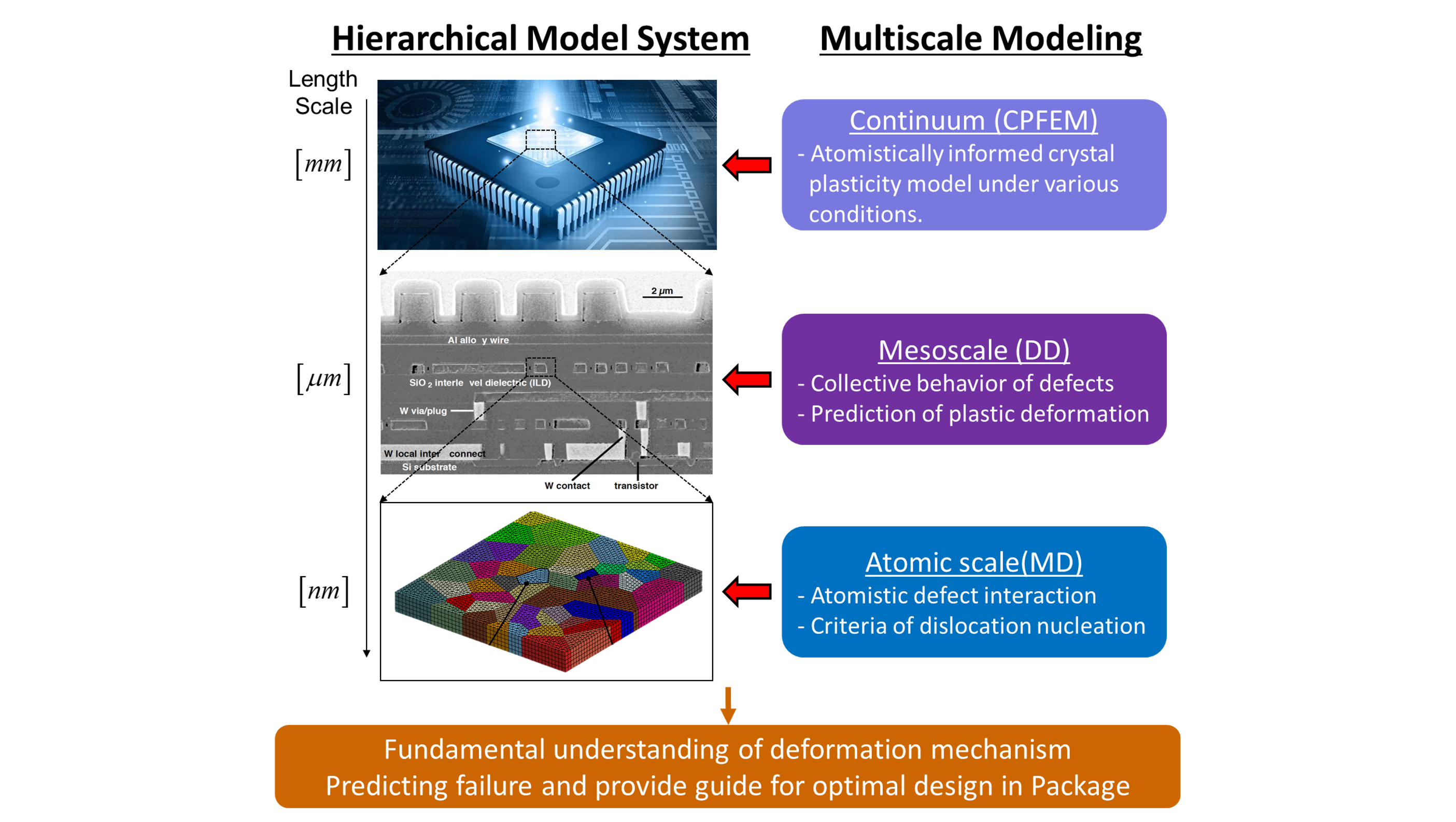
Reliability Analysis in Microelectronics
Mechanical Reliability analysis is dedicated to disseminating the latest research results and related information in microelectronic devices, circuits and systems, from materials, process and manufacturing. In our research, deformation and failure behavior will be investigated through consideration of defect microstructure, by multi-scale and multi-physical modeling approach for the reliable design of modern microelectronics.
Material Design
Data-Driven Property Optimization
High ductility and toughness are mutually contradicting properties and are challenging to be achieved simultaneously. Combining the vast component space of microstructure and the powerful high-dimensional data processing tools is expected to be the best solution to this problem. Using a multi-objective optimization driven by Machine Learning algorithm, we investigate the optimal design of defect microstructure.
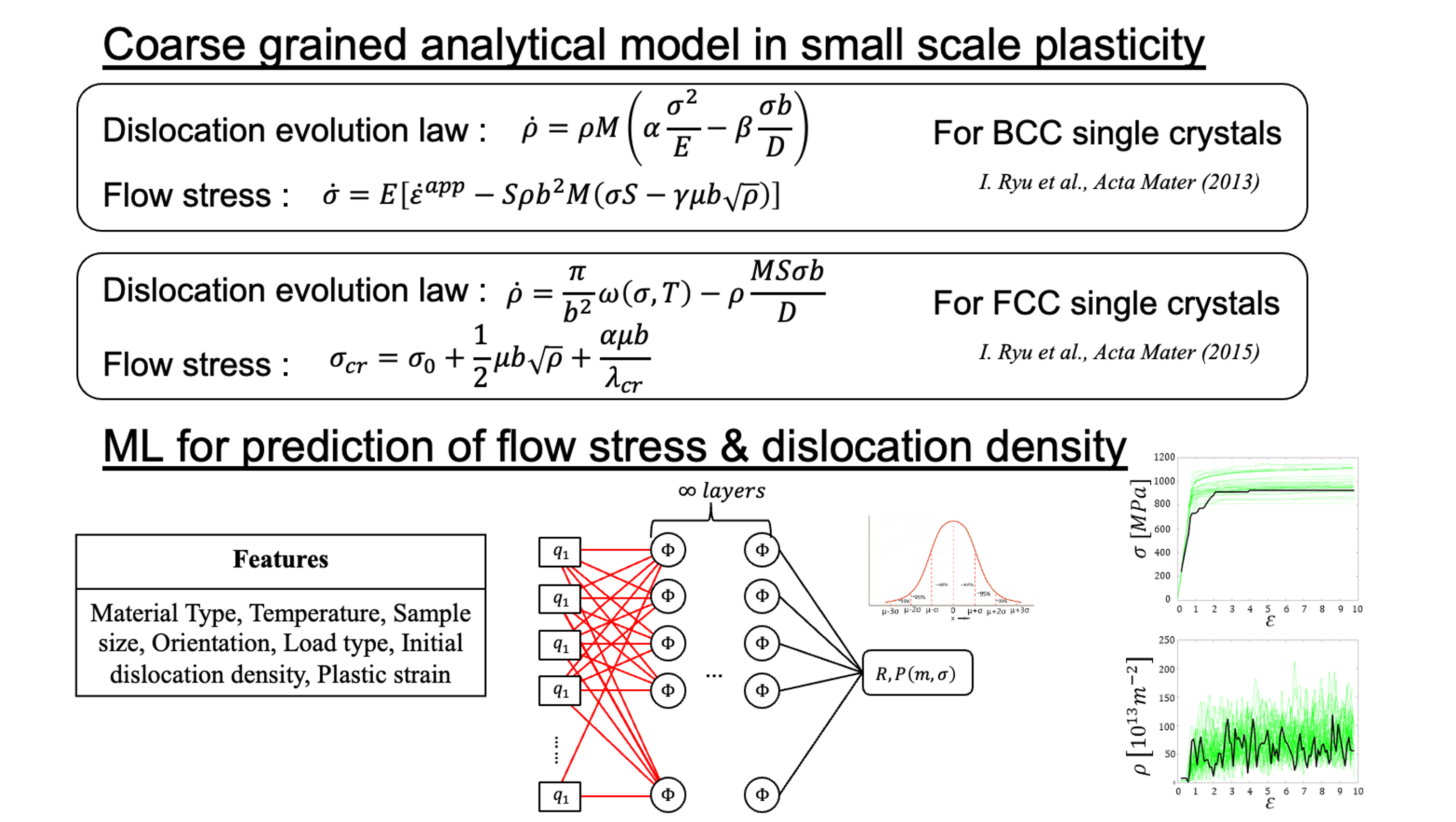